What is Surface Finishing?
Surface finishing means improving a material’s surface. You can achieve this by coating it or treating it chemically or mechanically. The goal of surface finishing is to improve materials’ aesthetics, durability, and functionality.
Coatings, like paint, powder coating, and electroplating, can improve a material’s look and performance. Mechanical processes, such as grinding and polishing, can also help.
Kindly learn about the comprehensive guide to floor finish in our other article.
The Importance of Surface Finishing
Surface finishing techniques are vital in many industries. These include automotive, aerospace, electronics, and construction. Proper surface finishing makes the product functional and pleasing to the eye.
It protects against corrosion. It helps materials resist wear over time. Also, a high-quality finish boosts products’ value and appeal.
For example, imagine buying a shiny new car only to find out that there are scratches on its paint job. These scratches hurt the vehicle’s curb appeal. If not fixed, they can cause corrosion.
In construction and aerospace, durability plays a critical role in ensuring safety. Any flaws in the surface finish could lead to catastrophic outcomes. Surface finishing is vital in many manufacturing processes.
It enhances functionality and aesthetics. It also protects against corrosion, which can degrade performance and reduce longevity. So, one should not undervalue it when making high-quality products.
Types of Surface Finishing
Surface finishing protects a product’s functionality and appearance. They must suit their intended purpose.
There are two main types of surface finishing techniques: mechanical and chemical. Each technique has specific applications, advantages, and disadvantages.
Mechanical Surface Finishing
Mechanical surface finishing uses mechanical energy to change a material’s surface. It alters the texture, shape, or size. You can achieve this finish by grinding, polishing, sandblasting, or shooting.
Grinding and polishing: It removes material from a workpiece. They achieve a smooth or mirror-like finish. Grinding removes a lot of material with abrasive wheels or belts. Polishing uses fine abrasives to create a glossy finish.
Sandblasting: It is an abrasive technique. It uses compressed air to propel sand, or other media, at high speeds against a surface. This process removes unwanted layers such as rust or paint from surfaces like metal or wood.
Shot Peening: Shot peening is a surface-finishing technique. It bombards the material’s surface with small spheres called shots. The impact creates small dents on the part’s surface. It compresses it to enhance its durability.
Chemical Surface Finishing
The process uses chemicals to improve the surface properties. It enhances functionality or appearance. This type of finish includes electroplating, chemical etching, and anodizing.
Electroplating is an electrochemical process. It deposits metal ions onto a conductive object. For example, manufacturers use it to apply copper plating on PCBs.
Anodizing is an electrolytic process. It creates a protective oxide layer on metals like aluminum. This improves corrosion resistance and adds color.
Electrically conductive etching uses acids or chemicals to remove parts of a surface. This creates patterns, textures, or designs. This technique is often used in decorative applications and creating small-scale parts.
It is vital to know the different surface finishing techniques. They affect a product’s look and function. Mechanical methods like grinding and shot peening increase durability.
They suit durable materials. Use chemical methods like electroplating or anodizing for better corrosion resistance and appearance.
Factors that Affect the Choice of Surface Finishing Techniques
Material Type and Properties
The choice of finishing technique will depend on the material being finished. Certain materials may require specific finishing techniques to achieve the desired result.
For example, metals often undergo electroplating or anodizing. This improves their corrosion resistance, wear resistance, and conductivity.
Plastics may be painted or coated to improve their durability and look. Also, hardness, ductility, and thermal conductivity affect the choice of surface finishing technique.
Hard materials, like tungsten carbide, need abrasive grinding. You can polish ductile ones, like aluminum, to a high shine. Also, high thermal conductivity materials, like copper, need special plating. These techniques might not suit other metals.
Desired Appearance and Functionality
Another key factor is the item’s desired look and utility. It has a significant effect on the choice of finishing procedure. Different finishes can give products different looks.
They can be matte, glossy, or reflective. It’s also important to consider color uniformity or variation. It helps to determine which finishing technique to use.
Functionality is key in choosing a surface finish. Different finishes provide different properties. Some improve wear resistance, while others boost electrical conductivity.
For instance, some coatings insulate. Others are for decoration only.
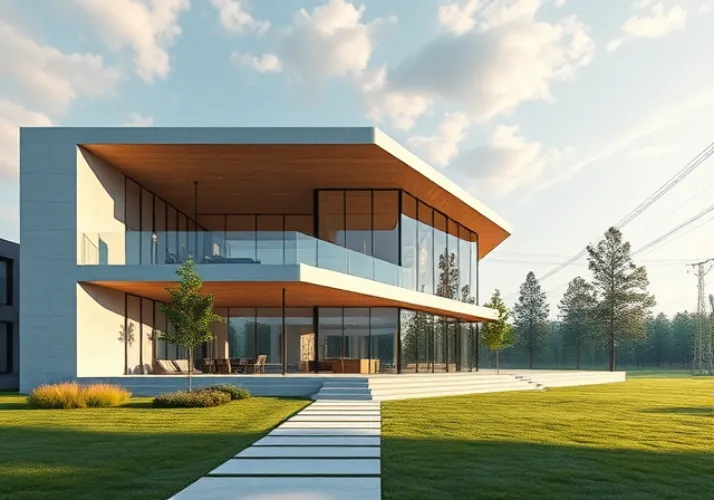
Environmental Considerations
When choosing a surface finishing technique, consider the environment. Due to regulations and public fears, environmental concerns are now more important.
People worry about pollution and waste. Some processes involve hazardous chemicals that need careful handling and proper disposal methods.
Also, to cut environmental impact during manufacturing, manufacturers should choose eco-friendly options. These should have low toxicity and use less energy.
Choose a surface finishing technique. It should consider its impact on the product and the environment.
Surface Preparation Techniques Before Applying the Finish
Cleaning process
Before applying any finish, it is vital to clean the surface. Cleaning removes dirt, oil, grease, rust, and other contaminants. They can harm the finish. There are two main types of cleaning: solvent and water.
Solvent cleaning
This is a process of utilizing solvents such as acetone, methanol, or ethanol to clean the surface. Solvent cleaners work well. It removes oils and other contaminants from metal surfaces.
They evaporate quickly. They leave a dry, clean surface for further work. Yet, solvent cleaning has some disadvantages.
Solvents are toxic, flammable substances. They can harm people and the environment if they are not handled perfectly. Moreover, solvents can damage some materials, such as plastics or paints.
Water cleaning
Water cleaning means using water to clean the surface. Then, dry it with hot air or a cloth. Water is a cheap, available solvent. It can remove most contaminants from metal surfaces.
However, water also has some drawbacks. It may not remove all contamination. So, for some uses, abrasive blasting or chemical treatment may be needed.
Surface preparation techniques
Once the surface is clean, it’s time to prepare it for finishing. Use one of several techniques, like abrasive blasting or chemical treatment.
Abrasive blasting
Abrasive blasting, or sandblasting, roughens surfaces. It’s done before applying finishes like paint or powder coating. It uses compressed air or water to spray abrasive particles at high speed onto a surface.
The abrasives used include silica sand, steel grits, and aluminum oxide among others.
Abrasive blasting textures the surface. It helps the finish stick and last longer. This strategy is commonly utilized in businesses like cars, aviation, and shipbuilding.
Chemical treatment
Chemical treatment is a process. It applies chemicals to a surface. This modifies its properties or removes contaminants. Different chemicals are used depending on the type of surface and its intended use.
For example, acid etching creates a rough surface. This helps paint and other finishes stick better.
Another common chemical treatment is phosphating. It applies zinc or iron phosphate. This creates a protective, anti-corrosion layer. Chemical treatment can increase the longevity of finishes and improve their appearance.
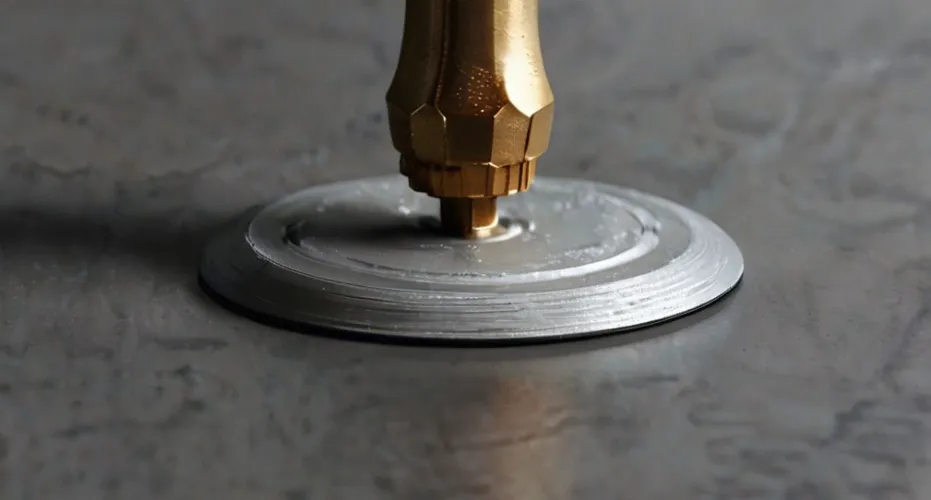
Application Techniques for Different Types of Surface Finishings
Electroplating Application Techniques
Electroplating is a process. It uses an electric current to deposit a thin layer of metal onto a surface. There are two popular electroplating techniques: immersion plating and brush plating.
Immersion plating coats an object by dipping it in a solution of dissolved metal ions.
The object is connected to the circuit’s negative terminal. The metal to be kept is connected to the positive terminal. A current flows through the circuit. It causes the metal ions in the solution to stick to the object’s surface.
Brush plating uses a handheld electroplating wand. It applies metallic coatings to specific areas of a terminal for precision. This technique is ideal for touching up small areas or repairing damaged surfaces.
Anodizing Application Techniques
Anodizing is an electrolytic process. It thickens and strengthens the natural oxide layers on aluminum and titanium. There are two common anodizing techniques: hard and decorative.
Hard anodizing creates a thicker oxide layer than normal anodizing. It does this by using higher voltages for longer periods.
It makes a hard, wear-resistant surface and can withstand extreme heat and harsh chemicals. This technique is often preferred for aerospace applications where durability is paramount.
Decorative anodizing, or color anodization, adds dyes to porous oxide layers. Standard anodization processes create these layers. The surface is vibrant.
Its colors won’t peel or chip. So, it’s ideal for consumer products like jewelry and kitchenware.
You can also read more on the best paint for your home in our other post.
Conclusion
Surface finishing processes are critical. They improve both the look and function of objects. Advancements in technology have created many application methods.
They can produce precise finishes with different durability and performance. Surface finishing is vital in manufacturing, for both commercial and consumer use. As technology advances, we can expect more innovations in the future.
If you found this article useful, kindly learn more examples of surface finishing processes here.